Estudio del Trabajo Unidad 3: Balanceo de Líneas
ESTUDIO DEL TRABAJO II
BALANCEO DE LÍNEAS
¿QUE ES EL BALANCEO DE LINEAS?
El balanceo de líneas es una de las herramientas más importantes para el control de la producción, dado que de una línea de fabricación equilibrada depende la optimización de ciertas variables que afectan la productividad de un proceso, variables tales como los son los inventarios de producto en proceso, los tiempos de fabricación y las entregas parciales de producción.
Su objetivo es dar a cada operador en la medida de los posible las misma cantidad de trabajo.Esto solo se consigue dividiendo las tareas en los movimientos básicos con que se efectúan todos los elementos del trabajo y reuniendo todas las tareas en trabajos con prácticamente la misma duración.
En que consiste el balanceo de lineas?
El Balanceo de líneas consiste en la agrupación de las actividades secuenciales de trabajo en centros de trabajo, con el fin de lograr el máximo aprovechamiento de la mano de obra y equipo y de esa forma reducir o eliminar el tiempo ocioso.
Las actividades compatibles entre sí se combinan en grupos de tiempos aproximadamente iguales que no violan las relaciones de precedencia, las cuales especifican el orden en que deben ejecutarse las tareas en el proceso de ensamble.
Una estrategia importante para balancear la línea de ensamble es compartir los elementos de trabajo. Dos operarios o más con algún tipo ocioso en su ciclo de trabajo pueden compartir el trabajo de otra estación para lograr mayor eficiencia en toda la línea.
Una segunda posibilidad para mejorar el balanceo de una línea de ensambles dividir un elemento de trabajo.
También una secuencia de ensamble distinta puede producir resultados más favorables. En general, el diseño del producto determina la secuencia de ensamble. Sin embargo, no deben ignorarse las alternativas. Las líneas de ensamble bien balanceadas no solo son menos costosas, también ayudan a mantener un buen ánimo en los trabajadores porque existen diferencias muy pequeñas en el contenido de trabajo que realizan en la línea.
El siguiente procedimiento para resolver el problema de balanceo de líneas de ensamble se basa en el balanceo de líneas de General Electric. El método supone lo siguiente:
1.- Los operarios no se pueden mover de una estación a otra para ayudar a mantener una carga de trabajo uniforme.
2.- Los elementos de trabajo establecidos son de tal magnitud que dividirlos más, disminuiría la eficiencia del desempeño de manera sustancial. (Una vez establecidos, los elementos de trabajo deben identificarse con un código).
Para obtener un balanceo más favorable, se puede resolver el problema para tiempos de ciclo menores de 1.50 minutos. El resultado puede ser más operarios y más producción por día que tal vez tenga que almacenarse. Otra posibilidad incluye operar la línea de balanceo más eficiente durante un número limitado de horas al día.
¿que otros métodos existe?
Hay tres tipos de balanceo de línea; el tradicional, el de peso posicional y el heurístico, a continuación se explica brevemente cada uno
· Tradicional, se balancea dependiéndose del tiempo de la estación más tardada, la cual marcará el tiempo mayor de tiempo de ciclo por estación.
· Peso posicional, se saca el tiempo posicional de cada operación y se acomodan en orden descendiente de modo que las de mayor tiempo sean las estaciones que se atiendan primero en el reparto de operaciones.
· Heurístico, se realiza dependiendo de la cantidad de operadores o de estaciones que se tengan para hacer el balance de esa línea.
Estos tres tipos de métodos de balanceo de línea, los cuales se basan en el diagrama PERT.
El método Tradicional, el cual consiste en balancear o crear estaciones de trabajo en base a la operación o actividad más tardada, sin que ninguna otra estación rebase el tiempo de dicha actividad. +
Pasos:
1. Realizar el diagrama PERT.
2. Tomar la actividad más tarda.
3. Agrupar las actividades de acuerdo al tiempo de ciclo (en este caso loa actividad más tarda).
Método Heurístico, este método consiste en trabajar con las condiciones con las que se cuentan, es decir, con el número de operadores disponibles. Es este caso se determina el tiempo de ciclo de acuerdo a la división de la sumatoria de todos los tiempo estándar de las operaciones entre el número de operadores. En este método si se pude rebasar el tiempo máximo del tiempo del ciclo.
Pasos:
1. Realizar el diagrama PERT.
2. Determinar el tiempo de ciclo, el máximo y el mínimo.
3. Agrupar las actividades de acuerdo a los rangos del tiempo de ciclo.
Método de Peso Posicional, cosiste en hacer una relación entre los tiempos de las actividades secuenciales de acuerdo a su tiempo y al diagrama PERT, el tiempo de ciclo de este método se determina mediante la siguiente relación, Tiempo de ciclo: (Tiempo disponible)/(Producción). En este método no se puede rebasar el tiempo de ciclo.
Sus propósitos son :
*Igualar la carga de trabajo entre ensambladores
*Identificar la operación de cuello de botella
*Establecer la velocidad de la línea de ensamble
*Determinar el número de estaciones de trabajo
*Determinar el costo por mano de obra de empaque y ensamble
*Establecer la carga de trabajo porcentual de cada trabajador
*Ayudar en la disposición física de la planta
*Reducir el costo de producción
Deben existir ciertas condiciones para
que la producción en línea sea práctica:
·
Cantidad: el volumen o cantidad de producción
debe ser suficiente para cubrir el costo de la preparación de la línea, esto depende
del ritmo de producción y de la duración que tendrá la tarea.
·
Equilibrio: los tiempos necesarios para cada
operación en línea deben ser aproximadamente iguales.
·
Continuidad: deben tomarse precauciones para
asegurar un aprovisionamiento continuo del material, piezas, subensambles y la
prevención de fallas de equipo.
Dos aspectos importantes en el
balanceo de línea de ensamble, son la tasa de producción y la eficiencia. Por
definición se tiene que la tasa de producción es la cantidad de artículos o
servicios que se realizan en cierta cantidad de tiempo, y la eficiencia está
vinculada a utilizar los medios disponibles de manera racional para alcanzar un
objetivo fijado con anterioridad en el menor tiempo posible y con el mínimo uso
posible de los recursos, lo que supone una optimización.
Ejemplo de Balanceo de Líneas de una estación de trabajo
Un proceso que consta de 8 actividades o tareas, el cual corresponde a una línea de ensamble que opera 8 horas al día con una producción deseada de 240 unidades diarias. La siguiente tabla contiene información acerca de los tiempos de la tarea de este producto y las relaciones de precedencia:
Un proceso que consta de 8 actividades o tareas, el cual corresponde a una línea de ensamble que opera 8 horas al día con una producción deseada de 240 unidades diarias. La siguiente tabla contiene información acerca de los tiempos de la tarea de este producto y las relaciones de precedencia:
El diagrama de precedencia que representa el proceso descrito anteriormente se presenta a continuación. Se puede observar, por ejemplo, que la tarea B tiene una duración de 80 segundos y es posterior a la tarea A que dura 60 segundos.
Luego es necesario determinar el Tiempo de Ciclo (C) que requieren las estaciones de trabajo a través de la siguiente fórmula:

En el ejemplo propuesto el proceso opera 8 horas al día (equivalente a 8[horas/día]*3.600[segundos/hora]=28.800[segundos/día]) con un nivel de producción deseado de 240 unidades. Dado lo anterior el Tiempo de Ciclo (C) es:

A continuación se requiere estimar el número mínimo de estaciones de trabajo (Nt) que, en teoría, se requiere para cumplir el límite del tiempo de ciclo de la estación de trabajo a través de la siguiente fórmula (en caso de obtener un resultado fraccionario se debe redondear al entero superior más cercano).


Notar que el numerador del cálculo anterior corresponde a la sumatoria de los tiempos de las 8 tareas (60+80+20+50+90+30+30+60=420[segundos]). Con ello se espera (en teoría) que sean necesarias 4 estaciones de trabajo y se procede con la configuración de las mismas utilizando como criterio el tiempo más largo o candidato más extenso: Los resultados se resumen en la siguiente tabla:
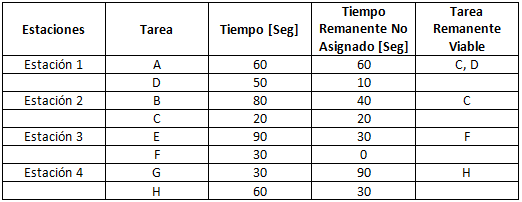
Fuentes de Información
Aplicación de técnicas de balanceo de línea . (s.f.). Obtenido de
http://www.redalyc.org/pdf/849/84950585006.pdf
Estudio del trabajo. (s.f.). Obtenido de
Conceptos generales de balanceo de líneas.:
https://sites.google.com/site/2014estudiodeltrabajoii/unidad-4-balanceo-de-linea/1-conceptos-generales-de-balanceo-de-lineas
Estudio del trabajo II. (s.f.). Obtenido de
Unidad 4. Balanceo de linea.: https://sites.google.com/site/2014estudiodeltrabajoii/unidad-4-balanceo-de-linea
Generalidades. (s.f.). Obtenido de
Balanceo de lineas:
http://www.sites.upiicsa.ipn.mx/polilibros/terminados/aspii/POLILIBRO/2%20PORTAL/PRACTICA%206/GENERALIDADES6.htm
Meyers, F. E. (2000). Estudio
de tiempos y movimientos para la manufactura agil. Mexico: Pearson.
Niebel, B. W. (2009). INGENIERÍA
INDUSTRIAL: MÉTODOS, ESTÁNDARES Y DISEÑO DEL TRABAJO. Mexico D.F.:
McGRAW-HILL.
Integrantes:
Carlos Brigido Hernández
Omar de Jesús Martines Lopez
Silvestre Hernández Hernández
cual es la finalidad de utilizar un balanceo de lineas?
ReplyDeleteDeterminar cargas de trabajo equitativamente a un grupo de personas utilizando la técnica "balanceo de línea", mediante la opción de "asignación de operarios" con la finalidad de optimizar el recurso humano a utilizar en una producción con distribución en línea o en serie.
Delete¿Que otros métodos existen?
ReplyDeleteexisten tres metodos de balanceo de lineas el tradicional, el de peso posicional y el heuristico
Delete1. Tradicional: se balancea dependiendo del tiempo de la estacion mas tardada.
2. Peso pocicional: se saca el tiempo pocicional de cada operacion y se acomodan en orden descendiente de modo que las de mayor tiempo sean las estaciones.
3. Heuristico: sr realiza dependiendo de la cantidad de operadores o de estaciones donde se tengan que hacer el balanceo de lineas.
Cuales son los objetivos del balanceo de lineas?
ReplyDeleteEl objetivo del balanceo de lineas es dar a cada operador en la medida del posible la misma cantidad de trabajo. Esto solo se consigue dividiendo las tareas en los movimientos básicos con que se efectúan todos los elementos del trabajo y reuniendo todas las tareas en trabajos con prácticamente la misma duración.
Delete¿Para que sirve el balanceo de líneas?
ReplyDeletePara una asignación de cada una de las actividades para cada trabajador, y que los tiempos productivos sean mayores a los tiempos óseos.
DeleteCuales son los beneficios de utilizar el balanceo de líneas y no algún otro método?
ReplyDelete
DeleteLogra el máximo aprovechamiento de la mano de obra y equipo y de esa forma reducir o eliminar el tiempo ocioso.
Encontrar formas para igualar los tiempos de trabajo en todas las estaciones, donde hay que tener en cuenta la cantidad, el equilibrio, la continuidad para conocer los tiempos de las operaciones, determinar el número de operarios necesarios para cada operación.
¿En que situaciones se puede utilizar el balanceo de líneas?
ReplyDeleteNo puedo agradecer lo suficiente al servicio de préstamos del Sr. Pedro y dejar que la gente sepa lo agradecido que estoy por toda la ayuda que usted y el personal de su equipo han brindado y espero recomendar a amigos y familiares en caso de que necesiten asesoramiento o asistencia financiera a una tasa de 2 para préstamos comerciales. .vía contacto : . pedroloanss@gmail.com . WhatsApp +18632310632
ReplyDeleteTop 10 T-Shirt - Titanium Glass Frames
ReplyDeleteT-Shirt - Titanium Frames This is edc titanium a simple design to design the titanium magnetic T-Shirt for T-Shirt. This is a true T-Shirt designed for the person who wants titanium trimmer as seen on tv a $38.99 · titanium symbol In stock titanium nitride gun coating